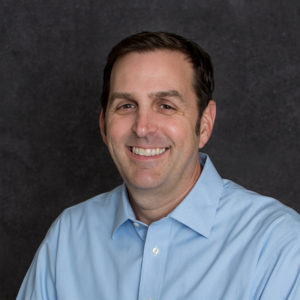
Audit Inspections and Findings: Recurring Issues with the Proper use of Type CE Continuous Flow Respirators during Abrasive Blasting Operations
Over the course of over twenty years of performing third-party health and safety audits of industrial abrasive blasting and painting contractors, I have noticed a recurring theme – respiratory protection plans are rarely properly implemented in accordance with the written plans that I have reviewed. In that same vein, annual evaluations that measure the effectiveness of the written plans by a qualified professional are rarely conducted. I am sure not many people will be surprised by this finding, yet this is a pervasive issue in the industry. I once had an owner of a painting firm ask me – Don’t you just put the respirator on and go to work? No. Many steps must be followed.
Whether it is lack of training, general apathy from those impacted in the industry about the topic, or some other reason, the ball, regarding complying with OSHA respiratory protection requirements, is being dropped.
The primary route of exposure for industrial abrasive blasters and painters is through inhalation. Therefore, failure to implement and evaluate one’s written respiratory protection plan increases the risk of those employees who are receiving an occupational exposure to particulates and vapors of developing an occupational injury and/or occupational illness.
Rather than delve into how to properly implement and evaluate a respiratory protection plan, I believe sharing the top recurring respiratory protection issues I have identified over the years with the use of Type CE Continuous Flow respirators (abrasive blast hoods) during abrasive blasting will provide more value. The top 7 issues are as follows:
TOP 7 Findings from Field Audits
1) Not ensuring Grade D breathing air
Grade D refers to breathing air quality established by the Compressed Gas Association (CGA G-7.1) that must be provided to those who wear the Type CE Continuous flow respirator. Issues related to Grade D breathing air for those using oil-lubricated compressors include:
- a) CO monitor was either not installed or if it was installed, it had not been calibrated;
- b) If using a high temperature alarm, it was not working properly, or if it is present, it had not been installed;
- c) Airline filter had not been installed, or the filter simply had not been changed out in accordance with the manufacturer’s recommendations.
2) Abrasive blast hood left in the containment
If you are one of those firms where this is a standard practice (Note: It is more common than you might think), consider that whatever you have been abrasive blasting off the steel structure, combined with the contents of the abrasive blast media, will settle into the respirator. When the compressor is started for the next shift, the abrasive blaster will receive an exposure to whatever has settled into the abrasive blast hood. From a logistics and cost standpoint, I understand why abrasive blast hoods are left inside of the containment. It appears to be a major pain to pull air hoses out of the containment – only to have to re-install them every shift. Nonetheless, blast hoods should never be left inside of containment.
3) Using more air hose length than specified by the manufacturer
It may come as a surprise, but there is a limitation on how many air hoses you can use. Always read and comply with the manufacturer’s user manual.
4) No pressure gauge present, or if there is one, it does not work
The air line respirator is only effective if it is used in accordance with the manufacturer’s specified pressure ranges. If there is no way to measure the pressure, there is no way to ensure you are using the respirator properly.
5) Inner shield is not being used
Abrasive blasters are notorious for taking out the inner shield -claiming they cannot see very well with it in place. The shield is there for a reason. Not using the respirator as it was designed could result in serious injury.
6) Modifying the Respirator
I have seen abrasive blasters on many occasions drill lights onto their hoods to help them blast – typically due to inadequate general illumination in the containment. You should never modify a respirator from how it was designed and certified. This includes adding and omitting components from the approved system.
7) Not using the approved air hose from the respirator manufacturer
You would not believe how often I hear people complain about this finding. The respirator was approved as a complete system. Therefore, the user must use the system and all of its approved components, as it was certified.
In closing, I do not want to appear as though I am picking on contractors. Many of them do an excellent job of protecting their workers and care genuinely about their welfare. The point of this article is to raise awareness that although we have come a long way as an industry in terms of protecting workers from health and safety hazards, we need to focus on issues like this so that we can control exposures to prevent the risk of occupational injury/illness.